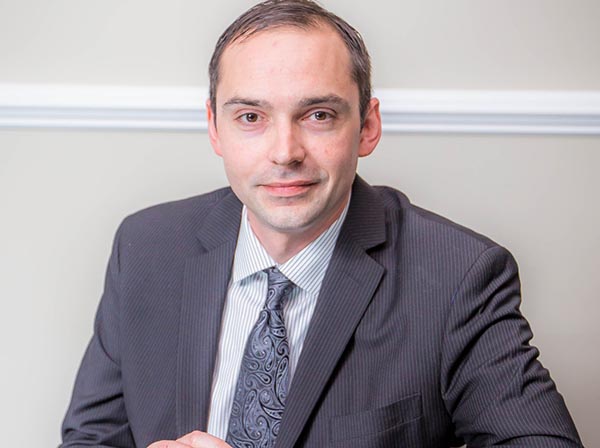
Click to learn more about author Aaron Fuller.
We got the power!
Well, figuratively speaking.
Manufacturers have the potential to be extremely powerful. Modern machinery – almost all of it – yields a tsunami of highly detailed data. The data can describe the function of the machine, errors that occur, how many things the machine built, how fast it built the things and so much more.
The trouble is, few manufacturers have a system for parsing and using that data in a meaningful way. A big reason for that is that it’s just so hard to wrap your arms around it all. You’re looking through 100 percent of the data to extract the 0.1 percent of information you need. It’s like looking at an entire atlas all at once, without even knowing your destination.
Drawing Your Map
Before you head down any road, it’s best to plan your route. Building your data integration infrastructure is like drawing your own map.
Raw data is your “Point A”; value is “Point B.” Along your path, you take that data and integrate it into your decision-making process to support manufacturing intelligence and analytics. Raw data has to be sourced from all the machines — i.e. identifying how and where each machine in your facility stores its data and getting the data out of that place. Then you need to take all the other internal systems where you have data and connect it to a central place where your internal data and your machine data can live together.
And that’s not it. Then you have to filter and summarize the data so it’s presented in a way people can use the data to understand what’s happening. Final step? Deliver the data insights to the people making decisions using dashboards, scorecards, alerts, reports and the like. The information you glean from those final data analysis tools gives you the insight you need to make decisions regarding what actions your business needs to take. Point A to Point B.
The “you” here doesn’t mean a person. It’s a system. Really, it’s a series of systems that all work together as a single support ecosystem.
That support ecosystem is essential groundwork to help you determine where to start gathering business insights – how does this one thing happening in our plant affect this other thing in our business?
Data can and should tell you, but you have to ask it first.
Understanding how to capture and analyze raw data from your machines, processes and operations and turning it into intelligent information you can use will absolutely save you time and money. And it will improve the quality of the work you do. Double bonus.
Understanding the Ecosystem
So, let’s define some of these systems that need to be developed and strung together:
- Data Lake: A data lake is where raw data from machines is collected. It’s also a place data analysts can explore what data is useful. It requires special infrastructure that could be installed on a server in-house or rented as a cloud service.
- Data Hub: The data hub is the centralized repository for useful data from the data lake, and your organization’s other important systems. Think sales data, CRM and accounting. It requires slightly different infrastructure than the data lake but it can also be run on a server or in the cloud.
- Data Warehouse: Your data warehouse is for storing information in a way that makes it easy to answer business questions. To get from a hub to a warehouse, you have to move the data and transform it by writing data integration systems. Many large manufacturers have whole departments that do this. Small- to mid-sized manufacturers may not, in which case you can explore consulting, vendor or contractor partnerships.
- Business Intelligence: The buzzword that just won’t go away. For manufacturers, BI refers to tools that display information and data visualization in the form of dashboards, scorecards, reports, etc. It tends to focus on trends and historic performance. You have to build business intelligence applications, but ultimately, BI is an ongoing discipline of refining the questions you ask and the human analysis of the information for continuous improvement.
- Analytics: In the manufacturing context, analytics refers to data analysis techniques that are more advanced than BI, especially those involving a lot of statistics. The other big difference between BI and analytics is that analytics tends to be focused on predicting the future, whereas BI is focused on understanding the past. This is where data scientists and predictive modelers and statisticians get involved to mine data out of all the systems mentioned above and use it to build analytic models to make valuable predictions.
Putting it to Work
Once the course is charted and you understand what the IT folks are actually talking about, it’s time to start digging in the data.
The most exciting possibilities for manufacturers lie in the data that the factory machinery generates, but all the rest needs to be in place to make good use of it. That’s why the data hub is an important stop along the way. It allows you to tie together the machine data and the business tools you use.
One of the most common problems we see in our manufacturing clients is a lack of good master data management for products, parts and machines. Often, they’re able to pull out a ton of individual machine information on their own, but turning that raw data into customized, relevant and actionable business information sometimes calls for an extra hand.
That work fuels the next step, which is key – using that data to leverage your most productive resources – whether that is machines or the productivity of people themselves – and improve the lower performers. Here’s where the data gets its power.
When manufacturers can forecast demand to meet a customer’s needs, they stay a step ahead of their competition. Understanding their machine utilization and downtime leads to more effective scheduling, which leads to a streamlined, efficient process. Understanding the way different workers use the machines can allow for coaching and training that improves results and employee satisfaction.
Plant managers will tell you this is their holy grail. Getting useful, thorough information about the workflow allows them to exploit the most potential from the machines, leading to skyrocketing value for your customers.
Making Better Decisions Through Data
Don’t worry about doing it all at once; build what you can afford to maintain and use it. If you don’t have an IT department with the in-house skills, look for partners — consultants, small businesses and supplier partners can get you headed in the right direction.
Regardless of how you get there, you do need to start going down this road. You need to make sense of your data if you want your manufacturing to make sense. And when you start to get a handle on it, the power of what manufacturers can do is amazing.