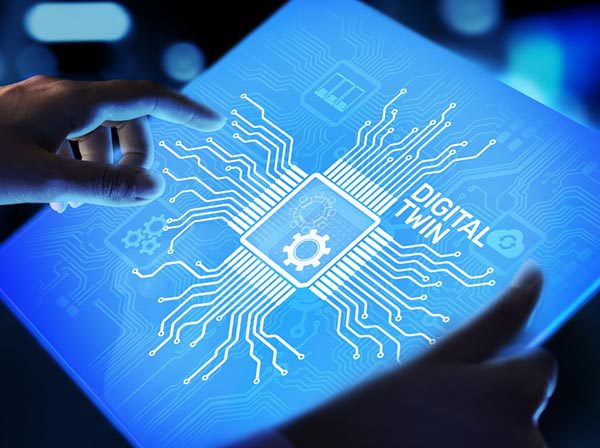
Digital twins can present a virtual replica of physical components, processes, or systems to enable improved understanding of the performance characteristics of such entities. With digital twins, industry operators can visualize, predict, and optimize the performance of individual components within a system or process, or the entire process from a remote location. According to Microsoft, the digital twin technology has converged internet of things (IoT), artificial intelligence (AI), and business analytics.
Data Science Trends in 2022 stated that the digital twin, which Gartner describes as the “mingling of the physical and digital,” has emerged as a groundbreaking new technology about to revolutionize all industrial processes.
The Meeting of the Physical and the Virtual
A Gartner article looks at some of the future prospects of digital twins. From the CIO’s vantage point, digital twins have the potential to create performance reports or drive pricing based on performance models. “Digital twins are the next step in the (IoT) driven world, where CIOs are increasingly leveraging IoT technologies in their journey.”
A Capgemini post makes an interesting case for the digital twin as a facilitator for “culture of continuous innovation” in an industry setting. As technology invades Industry 4.0, you may see an enhanced engagement of humans and machines via sensor data—the physical and the virtual coexisting happily.
IoT Has Catapulted the Use of Digital Twins
The IoT era has ushered in a seamless fusing of the “physical and the virtual worlds,” offering a unique competitive differentiation to enterprises. According to expert estimates, 20 billion devices will be sensor-driven by 2020. However, before organizations make costly technology investments, they need to revisit their current technology infrastructure to gauge the technology gaps in their systems.
Additionally, recent technologies like wireless sensors or edge computing enable advanced analytics to assess technology maturity. A Forrester Report describes how mobile app developers are using the IoT platforms and digital twins to accelerate design, development, and delivery of apps.
A NetworkWorld article makes a valid comparison between a product digital twin and a process digital twin, and provides concrete examples of how a process digital twin can benefit a product digital twin.
It reports that what makes digital twin simulations so realistic is the data that is gathered directly from real-world input channels. In an increasingly risk-averse but performance conscious business landscape, industry leaders and operators are excited about the possible business outcomes of using digital twins.
Digital Twins Are Revolutionizing Manufacturing Processes
As more manufacturing processes become sensor-driven and digitized, digital twins will play an important role in enabling an “under the hood” review of the individual components included in a manufacturing process.
A recent Gartner survey on IoT implementation states that 13 percent of organizations implementing IoT projects use digital twins, while 62 percent of organizations are in the process of implementing them. According to Benoit Lheureux, Research Vice President at Gartner:
“The results—especially when compared with past surveys—show that digital twins are slowly entering mainstream use. What we see here is that digital twins are increasingly deployed in conjunction with other digital twins for related assets or equipment.”
Digital twin integration activity is also on the rise; 61 percent of early implementers have “integrated at least one pair of digital twins,” while 74 percent of organizations who have not yet integrated digital twins propose to do so in five years.
In manufacturing, digital twins are currently being used as an industrial model to reveal the manufacturing defects and must also be periodically updated to reflect the usage degradation.
Another instance may be the use of digital twins to emulate the past and present behavior of a physical object with the intention of improving business performance. Digital twins are ideally suited to model highly digitized manufacturing processes.
Digital Twins: Enabling Next-Gen Manufacturing throws light on the obstacles faced by manufacturing industries as they move forward to embrace the “digital transformation.” What was around in product lifecycle management (PLM) for years has now emerged as a possible transformational technology for a manufacturing world with sensors and streaming data.
Other Industry Applications
In probable applications of this technology, the digital twin:
- Can serve as a functional prototype of a physical product, and can be monitored and assessed for performance improvements before the physical design.
- Can fully mimic an industrial process with all its constituent components to reveal the strengths and weaknesses of the entire process.
- Can even model the replica of a complete manufacturing unit, receiving real-time data from multiple data points.
- May be used to record consumer likes, dislikes, and preferences for improved recommendation services and customer support.
- Can provide direct interactions and data exchange between a physical entity and its digital replica to improve the performance of the physical object.
Enterprises often use these high-fidelity technology models to make decisions prior to actual product design, process implementation, or plant deployment.
Technology Benefits
A Digital Trends blog post offers these arguments in favor of implementing digital twins in a connected industrial setting:
Digital twins help to visualize how a remote product or process is actually functioning.
The digital twin creates a direct connection between the “physical” and its “digital” replica, thus making testing and monitoring the performance of the physical object via the replica possible.
Live data being the primary driver of a digital twin, data analysis and reporting are completed instantaneously.
Digital twins provide a “live demo” of actual performance metrics and earned business outcomes.
Finally, digital twin has accelerated the growth of IoT.
Modernizing Industries with an IoT-Powered Digital Twin confirms that the power of the digital twin lies in its ability to monitor performance or processes from afar, which is a game-changing concept for some industries like oil or gas.
The virtual model of a remote physical plant is especially useful in gauging the performance metrics with real-time or near-real-time data. John Vickers, manager of NASA’s National Center for Advanced Manufacturing, believes that “the ultimate vision for the digital twin is to create, test and build our equipment in a virtual environment.”
Image used under license from Shutterstock.com